Mit digitalen Werkzeugen die Produktion nachhaltig gestalten
Jahrzehntelang haben Kommerzialisierung und Globalisierung die Fertigungsunternehmen zu mehr Effizienz und Kosteneinsparungen getrieben. Inzwischen gewinnen jedoch die Umweltauswirkungen dieser Prozessentscheidungen zunehmend an Bedeutung. Im Bestreben, Kohlenstoffemissionen weltweit zu reduzieren, suchen Unternehmen nach Fortschritten, um dem Erfordernis der Nachhaltigkeit gerecht zu werden. Trotz jahrzehntelanger Investitionen in schlanke und effiziente Fertigungsprozesse verbraucht die globale Produktion immer noch enorme Energieressourcen (54 % weltweit) und verursacht ein Fünftel der weltweiten Kohlenstoffemissionen. Es wird eine Herausforderung sein, bis 2050 einen Netto-Nullverbrauch zu erreichen, und das ist nur eine Facette der Nachhaltigkeit. Unternehmen befassen sich darüber hinaus mit der Verbesserung der Ressourceneffizienz, des Energieverbrauchs und der Kreislaufwirtschaft. Und sie müssen diese Veränderungen in die Realität umsetzen und gleichzeitig die traditionellen Faktoren Zeit, Qualität und Kosten für ihre Produkte erfüllen.
Der herkömmliche Fertigungsansatz ist nicht geeignet, um diese zahlreichen Variablen auf dem Weg zu einer nachhaltigen Produktion zu berücksichtigen. Stattdessen bietet ein digitaler Zwilling, der neben anderen betrieblichen Parametern auch die Nachhaltigkeit berücksichtigt, die erforderlichen detaillierten Einblicke in den Produktionsprozess. Um erfolgreich zu sein, sollte dieser Ansatz die kollektive Intelligenz über die gesamte Wertschöpfungskette eines Produkts und dessen Lebenszyklus einbeziehen. Lösungen müssen über die Optimierung auf Werksebene hinausgehen und Daten über den gesamten industriellen Betrieb hinweg verknüpfen und analysieren – einschließlich der Ökosysteme von Lieferanten und Partnern. Dies alles auf einmal anzugehen ist nicht für jeden Hersteller machbar, geschweige denn für ganze Branchen. Daher ist es wichtig, einige der allgemeinen Konzepte zu verstehen, die auf dem Weg zu nachhaltigen Produktionsprozessen schrittweise umzusetzen sind.
Aus unserer Erfahrung als Hersteller und vertrauenswürdiger Partner von Kunden auf der ganzen Welt in fast allen Branchen gibt es vier Schlüsselbereiche, auf die sich die Industrie bei der Umstellung auf eine nachhaltige Produktion konzentrieren muss:
- Energieeinsatz
- Flexible Produktion und Innovation
- Service
- Planung und Optimierung von Produktionslinien
Jedes dieser Elemente für sich hilft bei der Realisierung eines rentablen und nachhaltigen Fertigungsunternehmens. Zusammengenommen machen sie Unternehmen zu Branchenführern.
Planung und Optimierung von Produktionssystemen
Änderungen an einer laufenden Fertigungslinie sind ein kostspieliges Unterfangen, wenn jede Sekunde, die im Leerlauf verbracht wird, mit Opportunitätskosten verbunden ist. Deshalb ist der digitale Zwilling der Produktionsumgebung ein so wertvolles Werkzeug. Mithilfe dieser virtuellen Darstellung des Werks oder der Fertigungsstraße können Ingenieure eine Vielzahl von Optimierungsmaßnahmen untersuchen, bis die optimale Lösung gefunden ist – und das, ohne die Produktion zu stören.
Darüber hinaus kann ein digitaler Zwilling zur kontinuierlichen Verbesserung bestehender Systeme beitragen, indem er reale Daten einbezieht, die mit Hilfe von Sensoren des industriellen Internets der Dinge (IoT) gesammelt wurden. Diese nutzt er dann, um die Leistung des physischen Systems in der digitalen Welt vorherzusagen und laufende Verbesserungen zu bestimmen. Die Analyse dieser Daten liefert eine virtuelle Darstellung der Prozesse und Maschinen, um Energie- und Produktionsdaten besser zu charakterisieren und zu kontextualisieren. Diese Art von Informationen stellt das kollektive Wissen von Anlagen, Fabriken und Unternehmen dar. Mithilfe dieses Wissens kann der digitale Zwilling eine kontinuierliche Optimierung umsetzen. Die Stärke des digitalen Zwillings liegt in seiner Flexibilität, mit der er auf nahezu jedes Nachhaltigkeitsziel in einer Produktionsumgebung angewendet werden kann – Energieeffizienz, Ressourceneffizienz, Langlebigkeit von Maschinen, Reparaturplanung, Inbetriebnahme neuer Anlagen usw. – für bessere Nachhaltigkeitsergebnisse.

Unser Kunde Hanson Cement war in der Lage, seine Niederspannungskühlsysteme digital zu optimieren und aufzurüsten, als diese sich dem Ende ihrer Lebensdauer näherten und weitaus energieeffizientere Motoren verfügbar waren. Zusätzlich zu den inhärenten Effizienzgewinnen der neueren Motoren im Kühlsystem wurde eine variable Drehzahlregelung eingesetzt, um den Kühlbedarf anzupassen und die Eingangsleistung des Systems detailliert zu minimieren. Die Umstellung funktionierte so gut, dass sie sich bereits nach wenigen Monaten durch die Energieeinsparungen amortisierte – etwa 86.000 Pfund (+- 100.500 Euro) an jährlichen Stromeinsparungen.
Verbesserung der Energieeffizienz
Der Energieverbrauch ist für die meisten Fertigungsunternehmen bereits eine wichtige Kennzahl, da er einen Großteil der Betriebskosten ausmacht. Die Senkung des Verbrauchs pro hergestelltem Produkt hat auch einen offensichtlichen Nachhaltigkeitsnutzen. Unabhängig davon, ob eine Fabrik Strom aus dem Netz oder Brennstoffe vor Ort für ihre Prozesse verwendet, entsteht ein entsprechender Kohlenstoff-Fußabdruck. Möglicherweise stehen die Unternehmen auch unter dem Druck, den Energieverbrauch zu verfolgen, zu optimieren und zu dokumentieren, um die ISO 50001-Normen zu erfüllen. Die Verbesserung der Energieeffizienz kann fast sofortige Vorteile bringen, indem sie die Gesamtkosten und den Kohlenstoffausstoß reduziert. Da viele Unternehmen bereits mit der Verwaltung technischer Anforderungen vertraut sind, ist es ein Leichtes, diese Prozesse im Bereich der Nachhaltigkeit zu implementieren.
In Europa steht die Energieeffizienz angesichts des Anstiegs der Energiekosten besonders im Fokus. Als Reaktion darauf setzen einige Unternehmen als Teil eines digitalen Systemansatzes intelligente Antriebssysteme ein, die den Energiebedarf um bis zu 60 % senken. Andere investieren darüber hinaus in unternehmensweite Energiemanagementlösungen, um die Quellen des größten Verbrauchs zu ermitteln und sie in absteigender Reihenfolge zu beseitigen. Noch mehr Unternehmen setzen Produktionsüberwachungssysteme ein, um das Lastmanagement zu automatisieren, indem sie Geräte abschalten oder im Leerlauf betreiben, wenn sie nicht in Gebrauch sind.
Einer unserer Großkunden aus der Lebensmittel- und Getränkeindustrie hat beispielsweise den Energieverbrauch in einer einzigen Anlage um 13 Prozent gesenkt und im ersten Jahr 110.000 Euro durch Verbesserungen der Anlageneffizienz eingespart. Wir halfen ihm bei der Implementierung einer digitalen End-to-End-Lösung, die seine Maschinen und Fabriksensoren mit Edge- und Cloud-Systemen für den Betrieb verbindet. Zusätzlich zu den Energieeinsparungen kann das Unternehmen nun auch eine besser vorausschauende Wartung durchführen, um Ausfallzeiten in Notfällen nahezu auszuschließen.
Aufbau einer flexiblen Produktion
Flexibilität und Effizienz gehen Hand in Hand. Wenn man in der Lage ist, sich schnell umzustellen und mit den vorhandenen Produktionsmitteln an neue Marktbedingungen anzupassen, lässt sich Verschwendung erheblich reduzieren. Die Weiternutzung vorhandener Maschinen und Anlagen ist ein großer Vorteil, um Nachhaltigkeitsziele zu erreichen. Diese Flexibilität kann durch innovative Fertigungsverfahren wie die additive Fertigung erreicht werden, aber auch durch eine Makrolösung, wie sie in der modularen Produktion zu finden ist. Beide Lösungen für eine flexible Produktion ermöglichen es, dass Anlagen leichter umgerüstet oder neu konfiguriert werden können, um jedes beliebige Produkt in jeder Produktionsstätte auf der ganzen Welt herzustellen.
YOU MAWO ist ein großartiges Beispiel für die Nutzung der Flexibilität der additiven Fertigung und die Erzielung von Nachhaltigkeitsvorteilen. Mithilfe einer vollständigen digitalen Zwillingsmethodik für Fertigung, Nachbearbeitung, Materialhandhabung und Logistik ist das Unternehmen in der Lage, seinen Kunden maßgeschneiderte Brillen zu liefern. Die Brillengestelle werden 3D-gedruckt, um sie optimal an die Gesichter der Kunden anzupassen und den Materialbedarf für die strukturelle Festigkeit zu minimieren. Diese Entscheidungen führten zu einem um 58 Prozent geringeren CO2-Fußabdruck im Vergleich zu herkömmlichen Brillengestellen, da Material eingespart, die Markteinführung beschleunigt und die künftige Produktion skaliert werden konnte.
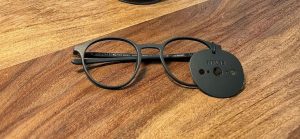
Förderung der Dienstleistungstechnik
Die Verbesserung der Langlebigkeit von Anlagen ist ein weiterer wichtiger Schwerpunkt bei der Schaffung nachhaltiger Produktionsumgebungen. Auch hier ist das Konzept für die Hersteller nicht neu. Der Austausch von Maschinen ist eine teure Angelegenheit, aber auch die Durchführung von Reparaturen in letzter Minute. Durch die Digitalisierung dieser Systeme können die Wartungszyklen in Bezug auf Zeit und Ressourcen effizienter gestaltet werden. Ein industrielles IoT-System, das mit dem digitalen Zwilling der Fertigungslinie verbunden ist, kann den Bediener darüber informieren, wenn eine Maschine unter einen bestimmten Effizienzschwellenwert gefallen ist und sich auf den Energieverbrauch, die Produktionskapazität, die Sicherheit der Mitarbeiter oder eine beliebige Anzahl von wichtigen Betriebskennzahlen auswirkt.
Die Verbindung mit dem digitalen Zwilling ermöglicht eine Vorhersage der Auswirkungen dieser Änderungen. So kann die Wartung von einem reaktiven Vorgang zu einem bewussten Prozess werden. Ein Unternehmen könnte eine fehleranfällige Komponente während der erwarteten Ausfallzeiten reparieren, ersetzen oder die Prozesse anpassen, um die Ausfallwahrscheinlichkeit der Komponente zu minimieren. Die Betrachtung dieser Maschinen als langfristige Plattformen bietet Unternehmen einen weiteren Weg zu einer nachhaltigen Produktion. Anstatt Maschinen als Wegwerfanlagen zu betrachten, bietet die Aufrechterhaltung ihrer Betriebsbereitschaft mehr Investitionsmöglichkeiten in die anderen Konzepte der nachhaltigen Fertigung.
Beispiel aus der Praxis: einsatzfähige nachhaltige Produktionslösungen
Während sich viele digitale Werkzeuge zur Verbesserung der Nachhaltigkeit in der Fertigung noch im Anfangsstadium befinden, hat Siemens sie alle in einer einzigen digital-nativen Fabrik in Nanjing, China, zusammengeführt. Das Werk von Siemens Numerical Control (SNC) stellt hochwertige numerische Steuerungssysteme, Antriebe und Motoren her und wurde zu einem digitalen Unternehmen, als drei Produktionsstandorte zu einer nachhaltigen Fabrik zusammengelegt wurden.
Mit den oben beschriebenen Ansätzen erzielten sie einige bemerkenswerte Ergebnisse:
- Verdoppelung der Produktionskapazität
- Steigerung der Effizienz um 20 Prozent
- Verbesserte Flexibilität um 30 Prozent
- Verkürzung der Markteinführungszeit um 20 Prozent
- Steigerung der Flächennutzung um 40 Prozent
- Verbesserte Effizienz des Materialflusses um 50 Prozent
Ebenso wichtig ist, dass die SNC-Anlage die werksweiten Emissionen durch Erdwärmepumpensysteme und Fotovoltaikanlagen weiter reduzieren konnte, während die energieintensivsten Maschinen in der Fertigung zugunsten neuerer Modelle stillgelegt wurden.
Der Aufbau nachhaltiger Produktionsunternehmen wird zu einer Grundvoraussetzung eines Betriebs. Die Umsetzung ist der nächste wichtige Schritt, um das Potenzial auszuschöpfen. Es ist wichtig zu verstehen, dass Nachhaltigkeit keine nachträgliche Lösung für bestehende Prozesse ist. Sie muss bei jeder Entscheidung während des gesamten Produktlebenszyklus und innerhalb des Ökosystems berücksichtigt werden. Glücklicherweise sind viele der besten Ansatzpunkte zur Nachhaltigkeit bereits als Gewinnanreize in den heutigen Fertigungsunternehmen vorhanden und wir werden auch weiterhin dabei helfen, die digitalen Werkzeuge zu entwickeln, die dies möglich machen.
Wenn Sie mehr über unsere Arbeit für mehr Nachhaltigkeit erfahren möchten, besuchen Sie unsere Website.
Um einen Kommentar zu hinterlassen müssen sie Autor sein, oder mit Ihrem LinkedIn Account eingeloggt sein.