In modernen Fabriken ist der Roboter der ideale Mitarbeiter. Er arbeitet rund um die Uhr ohne zu ermüden und erledigt seine Aufgaben mit hoher Geschwindigkeit und Präzision, was die Durchlaufzeiten verkürzt und damit die Produktionskapazität erhöht. Seine Fähigkeiten sind nahezu unbegrenzt und reichen von einfachen, sich wiederholenden Tätigkeiten bis hin zu komplexen Arbeiten. So be- und entladen Roboter Maschinen und Förderbänder, transportieren Materialien innerhalb der Fabrik und übernehmen die präzise Montage von Bauteilen einschließlich Nieten und Schrauben. Auch Schneiden und Fräsen, Löten und Schweißen, Schleifen, Lackieren und Emaillieren gehören zu ihren Aufgaben in einer modernen Fabrik.
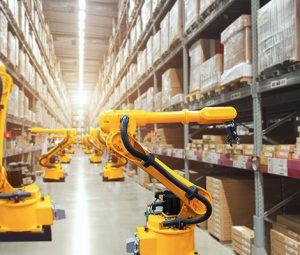
Digitaler Zwilling perfektioniert Prozesse
Im Qualitätsmanagement wiederum messen, prüfen und analysieren mit Kameras und Sensoren ausgestattete Roboter Ist- sowie Soll-Zustände und stellen so sicher, dass die Produkte den geforderten Spezifikationen entsprechen. Sie überwachen zudem den Zustand von Anlagen und Fertigungsstraßen, prognostizieren fällige Wartungsarbeiten und führen sogar einfache Reparaturen an anderen Maschinen durch. Einen Schritt weiter gehen die sogenannten Cobots – der Begriff steht für Collaborative Robots, also Maschinen, die Hand in Hand mit dem Menschen arbeiten. Im Gegensatz zu herkömmlichen Industrierobotern, die oft in abgeschlossenen Bereichen agieren, um die Arbeitssicherheit zu gewährleisten, sind Cobots so konstruiert, dass sie intelligent auf ihr Umfeld reagieren und eigenständig Entscheidungen treffen – zumindest soweit es ihre KI zulässt.
Ohne modernste Technologien funktioniert diese neue Produktionswelt jedoch nicht. Alle Systeme, von der Fräsmaschine über den Fließbandroboter bis hin zum vollautomatisierten Lager, müssen relevante Informationen aus den gesammelten Daten an die OT- und IT-Systeme weiterleiten – nur dann ist die Erfassung des aktuellen Zustands einzelner Fertigungsstraßen oder kompletter Fabriken möglich. Wird ein digitaler Zwilling eingesetzt, lässt sich sogar die Fertigung ohne Unterbrechung des laufenden Produktionsprozesses simulieren und optimieren. Dieses virtuelle Abbild eines physischen Objekts oder Systems spiegelt den Zustand und die Funktion seines physischen Gegenstücks in Echtzeit wider, indem es Daten von Sensoren und anderen Quellen analysiert. Mit dem digitalen Zwilling können also Prozesse simuliert, überwacht und optimiert werden, ohne die physische Umgebung zu beeinträchtigen. So können die Betriebe beispielsweise Produktionsumstellungen auf andere Modelle oder kleinere Serien vorab durchspielen sowie die Fertigung eines Einzelstücks mit vorgegebener Genauigkeit auf verschiedenen Fertigungsstraßen simulieren und dann die dafür geeignetste Maschine auswählen. In letzter Konsequenz lässt sich ein bidirektionales System umsetzen, bei dem der digitale Zwilling seinem physischen Bruder Rückmeldungen gibt und sich folglich selbst steuert.
Edge Computing und 5G liefern die technologische Basis
Alle Anwendungsszenarien haben eines gemeinsam: Durch die unterschiedlichsten Sensoren fallen enorme Datenmengen an, die möglichst schnell ausgewertet werden müssen. Die technologische Basis oder besser gesagt die Grundvoraussetzung dafür sind Edge Computing und 5G. Mit Edge Computing verlagert sich die Verarbeitung von Daten näher an den Ort ihrer Entstehung – in diesem Fall direkt in die Fabrikhalle. Anstatt große Datenmengen an zentrale Rechenzentren zu senden, wo der Transport zusätzliche Zeit in Anspruch nimmt, werden die Informationen lokal mithilfe von Analysealgorithmen und vor-trainierten KI-Modellen ausgewertet. Dies nutzt die geringe Latenz in lokalen Netzen und ermöglicht schnellere Reaktionszeiten, was insbesondere in der Fertigung mit ihren autonom agierenden Robotern von entscheidender Bedeutung ist. Ohne Echtzeit-Analyse wären beispielsweise fehlerhafte Produkte auf dem Band weitergewandert, bevor ein Roboterarm das entsprechende Teil überhaupt aussortiert hätte. Alle erfassten Daten werden zudem aggregiert, sodass nur noch die abgeleiteten Ergebnisse zur weiteren Verarbeitung oder Langzeitspeicherung an einen zentralen Ort zum Beispiel in der Cloud gesendet werden. Die Edge wird damit zum Bindeglied zwischen der realen Welt und ihrem digitalen Zwilling.
Die andere Schlüsseltechnologie für die moderne Fabrik ist 5G. Die Mobilfunknetze der neuesten Generation bieten maximale Datenraten von zukünftig bis zu 20 Gbit/s bei extrem niedrigen Latenzen. Gleichzeitig können sehr viele Geräten eingebunden werden. Darüber hinaus wird 5G Time Sensitive Networking (TSN) unterstützen, das unter anderem für die synchrone Kommunikation zwischen Sensoren, Maschinen und Steuerungssystemen genutzt wird und damit exakt aufeinander abgestimmte Abläufe ermöglicht. Nicht zuletzt hat 5G gegenüber anderen Funktechnologien einen weiteren durchaus relevanten Vorteil: Der Mobilfunkstandard unterstützt ein nahtloses „Handover“ beim Wechsel von einer Funkzelle in eine andere. Gerade in Fertigungshallen und Lagern kommt es immer wieder zu solchen Übergängen, da dort aufgrund von Wänden oder Metallkonstruktionen für eine durchgängige Funkabdeckung mehr Basisstationen aufgestellt werden müssen als auf freien Flächen. Bei der Verwendung anderer Funktechnologien besteht das Risiko, dass fahrerlose Transportfahrzeuge oder Roboter beim Zellenwechsel kurzzeitig die Verbindung verlieren – mit weitreichenden Folgen für Produktionsabläufe und Mitarbeitersicherheit.
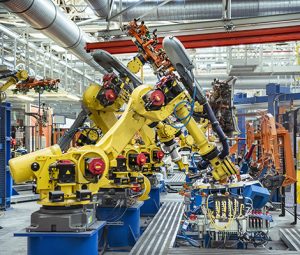
Bei der Realisierung der smarten Fabrik lauern Stolpersteine
Die Umsetzung dieser neuen Produktionswelt ist alles andere als trivial – schließlich gilt es, gleich mehrere Herausforderungen zu meistern. Die umfassende Einbindung von Produktionsmaschinen, Sensoren und Gateways in das Netz sowie das Ausrollen verteilter Edge-Server in der Fläche erfordern zunächst nicht unerhebliche Investitionen, die sich erst mittelfristig auszahlen. Die Einführung der verschiedenen Technologien setzt zudem ein tiefes Verständnis und Know-how voraus, über das nur wenige Unternehmen verfügen oder für das ihnen die Ressourcen fehlen. Mit der zunehmenden Vernetzung steigt auch das Risiko von Cyberangriffen. Daher ist ein umfassendes Security-Konzept einschließlich Verschlüsselung, Zugangskontrollen und kontinuierlicher Überwachung unerlässlich, um die Integrität der Systeme und Daten zu schützen. Gelangen produktionskritische Informationen in die falschen Hände, drohen der Verlust von geistigem Eigentum und der Stillstand von Produktionsanlagen. Bei einem öffentlichen 5G-Netz verlieren Unternehmen schnell die Hoheit. Private 5G (P5G), also ein in sich geschlossenes Netzwerk, ermöglicht hingegen die Umsetzung individueller Maßnahmen und die Speicherung sensibler Daten direkt vor Ort. Angesichts all dieser Herausforderungen kann ein As-a-Service-Modell eine – auch wirtschaftlich – sinnvolle Lösung sein. Mit einer verwalteten Edge-Computing-Plattform sind Unternehmen in der Lage, Anwendungen schneller zu implementieren und produktiv zu nutzen. Gleichzeitig fungiert der Systemintegrator je nach Bedarf als zentraler Ansprechpartner für den End-to-End-Betrieb.
Fakt ist: Die enge Integration von Robotern und digitalen Zwillingen in modernen Fabriken schafft eine dynamische und adaptive Produktionsumgebung. Roboter profitieren von den präzisen Analysen und Optimierungen ihres digitalen Abbildes, während die digitalen Zwillinge durch die Echtzeitdaten und Erfahrungen der Roboter kontinuierlich verbessert werden. Dieses Zusammenspiel führt zu einer signifikanten Steigerung der Effizienz, Flexibilität und Qualität in der Fertigung, was letztendlich den Weg zur voll vernetzten, intelligenten Fabrik der Zukunft ebnet.
Um einen Kommentar zu hinterlassen müssen sie Autor sein, oder mit Ihrem LinkedIn Account eingeloggt sein.